An angle grinder, sometimes called a disc grinder or side grinder, is a hand-held power tool designed for rough grinding and polishing surfaces. Although originally developed as tools for tough edged abrasive discs, their availability of a versatile power source has encouraged their wide use in a variety of cutting and polishing applications. The angle grinder can be used with a variety of power tools, such as bench knives, hand drills, power drills, as well as on machine-operated lathes. Most modern angle grinders are in one of two types: handheld angle grinders and stand mounted grinders. While both types of angle grinder have similar power and pace, they differ primarily in the method of operation.
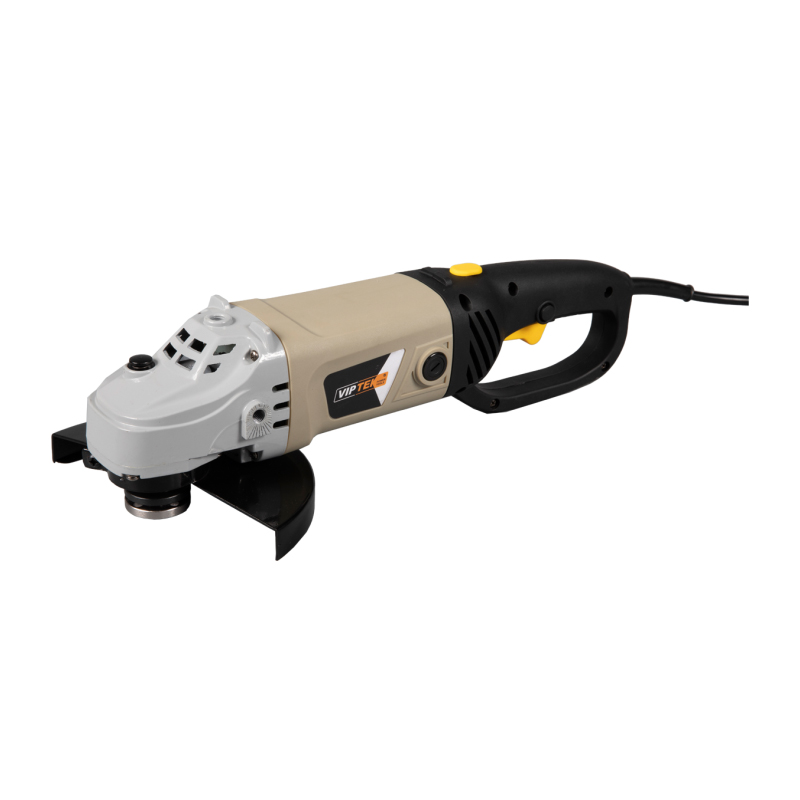
Handheld angle grinders are compact and versatile tools. They have large flat disks and a large chuck that spin around and are used to deposit material. Unlike some other types of grinding tools, the larger disc wheeled by its own motor is capable of spinning at a very high speed. The large disc produces a coarse texture and a coarse finishing finishing rough edges.
Many industrial applications require the use of steel angle grinders for rough finishing on metal surfaces, especially stainless steel and iron. The steel wheels can be used to roughen metals during the finishing process, as well as to polish them. Some angle grinders have anvils that are used to transfer material to another location, such as to a plasma cutter or an electrochemical torch. Other types of grinding wheels are used in applications where sharp abrasives are needed, for example in the making of stainless steel sinks, in welding and cutting processes, or in chemical and biological applications. In addition, some specialty types of wheeled angle grinders are sometimes used in the electronics industry, such as in automated welding processes.
The two types of grinding wheels are similar but there are significant differences. The first type is a CNC which stands for "Computer Numerated Control" machine. This is a fancy way of saying that the angle grinder is controlled by a computer through a series of computer instructions. The second type of wheel is called the flap disc type. Flap discs are designed to do the same job as CNC machines, but they have fewer moving parts. They are also easier to repair and keep working, since they tend to have fewer moving parts.
When working with abrasives, a CNC angle grinder will normally come equipped with both a sanding flap disc and a grinding wheel. Usually one or the other of these will be required. In most cases, both of them are interchangeable. A sanding flap disc is used to remove a small amount of material to get to the rough or finished surface of the abrasive. A grinding wheel, on the other hand, is used to grind or polish the surface of the abrasive to make it smooth.
With CNC machines, the roughing of the metal before polishing is done automatically. The discs that are used in this process are often made out of a hard, solid steel alloy. Some abrasives, such as aluminium oxide, are used to give the metal impregnated shine. In all cases, however, stainless steel discs are preferred because they are non-conductive and therefore will not tarnish when exposed to the elements.
There are many other types of machining tools that can be used to perform a variety of different types of operations. If you are interested in purchasing angle grinders and other types of tools, you should speak to your local machining supply store. Most stores will carry a large selection of discs and other tools needed to complete various types of projects.
CNC angle grinder owners often find themselves using a CNC machine in applications other than grinding. When a wheel is broken in a lathe, for example, the owner can often replace the broken wheel by installing another with the same specifications as the original. This allows the business owner to continue to service his or her equipment. It also helps to cut down on waste because one wouldn't have to worry about disposing of the broken disc after the wheel has been replaced with a new one.